Can we really get 60, 000 parts in one day?
We talked to Spenser Loveless from Merit3D. They have a factory full of resin 3D printers which they use to create parts for mass production.
With a recent project, one of his machines was able to print 800 parts in one print.
Multiply that by all his machines and Merit3D printed 60, 000 parts in one day.
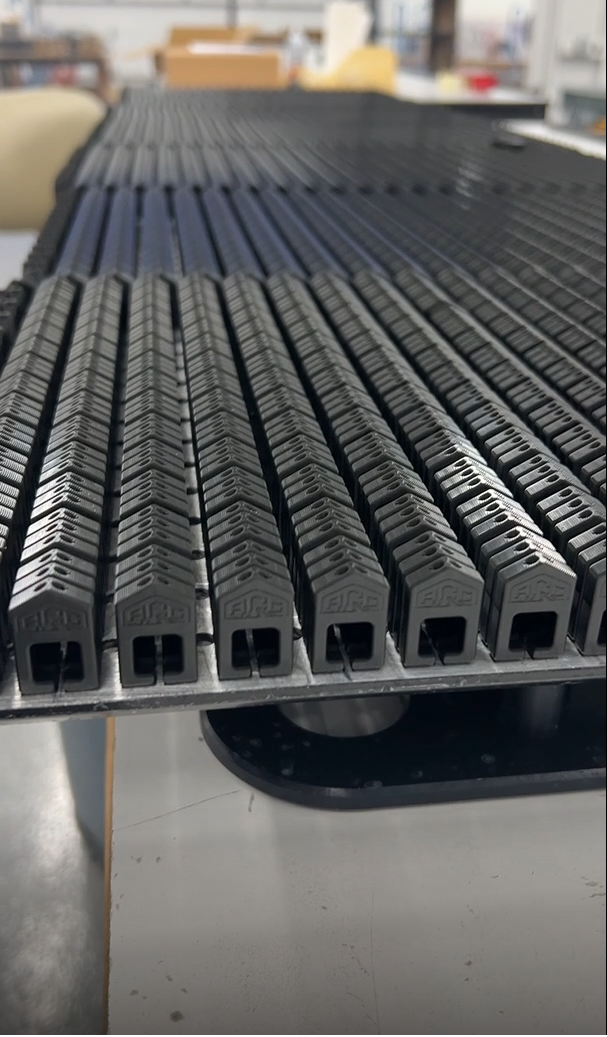
All this without spending $30 000 on an injection mould.
Have a look at the part here: alaskaguidecreations.com
Obviously, you have to take into consideration the initial cost of the 3D printers. Merit3D has spent the money already and gone through the teething problems so his customers don’t don't need to.
Mass Production using Resin 3D printing
What is Resin 3D Printing?
In a massively simplified nutshell, resin 3D printing has 3 major components
1. Tray of resin
2. Platform
3. LCD Projector.
These components 'print' the 3D part. Layer by layer.
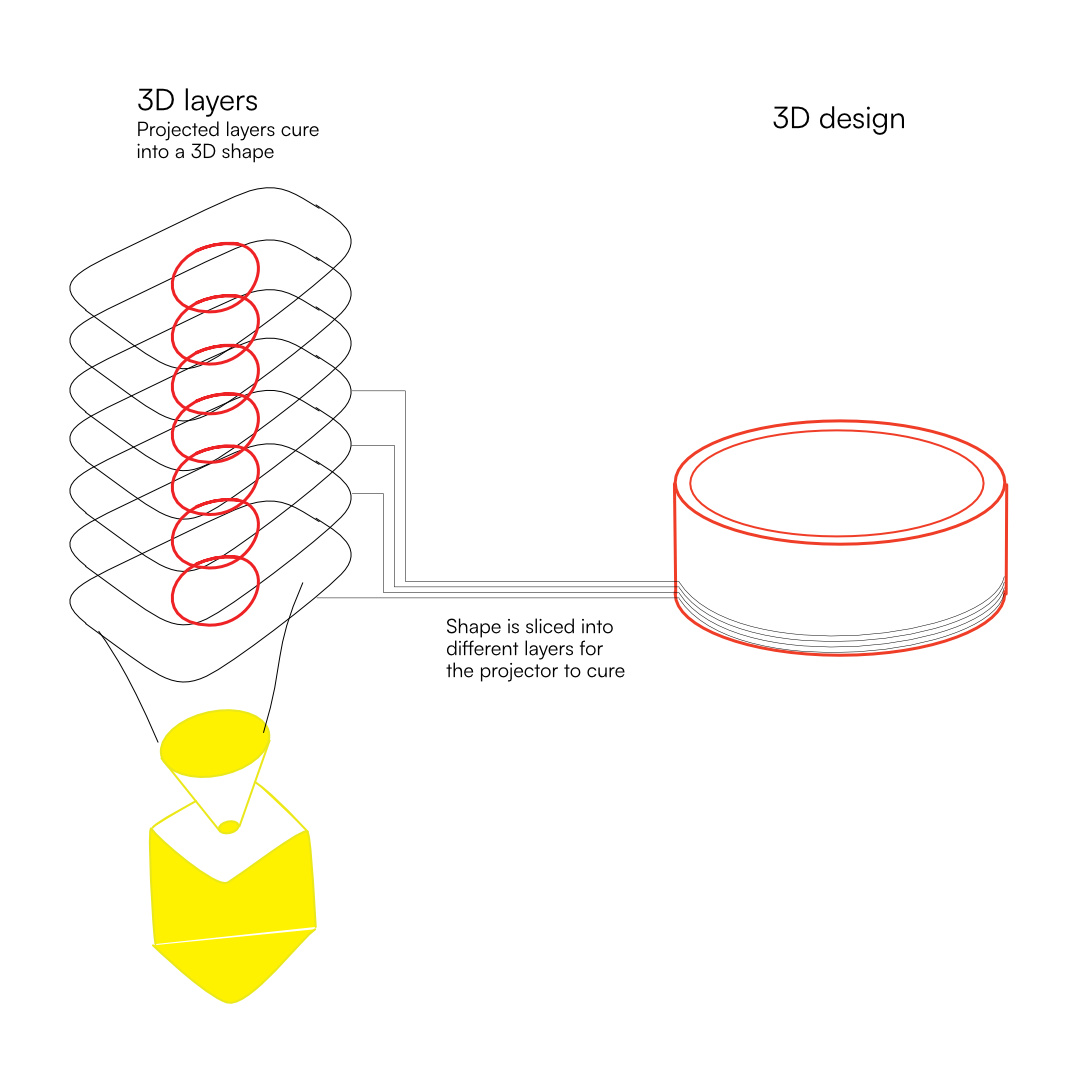
If you’ve ever watched a medical show using an MRI machine. They record data in thin sections. Now imagine you could reverse an MRI machine and use it to grow a human. One thin layer at a time. That's 3D printing! The shape is grown in one thin layer at a time.
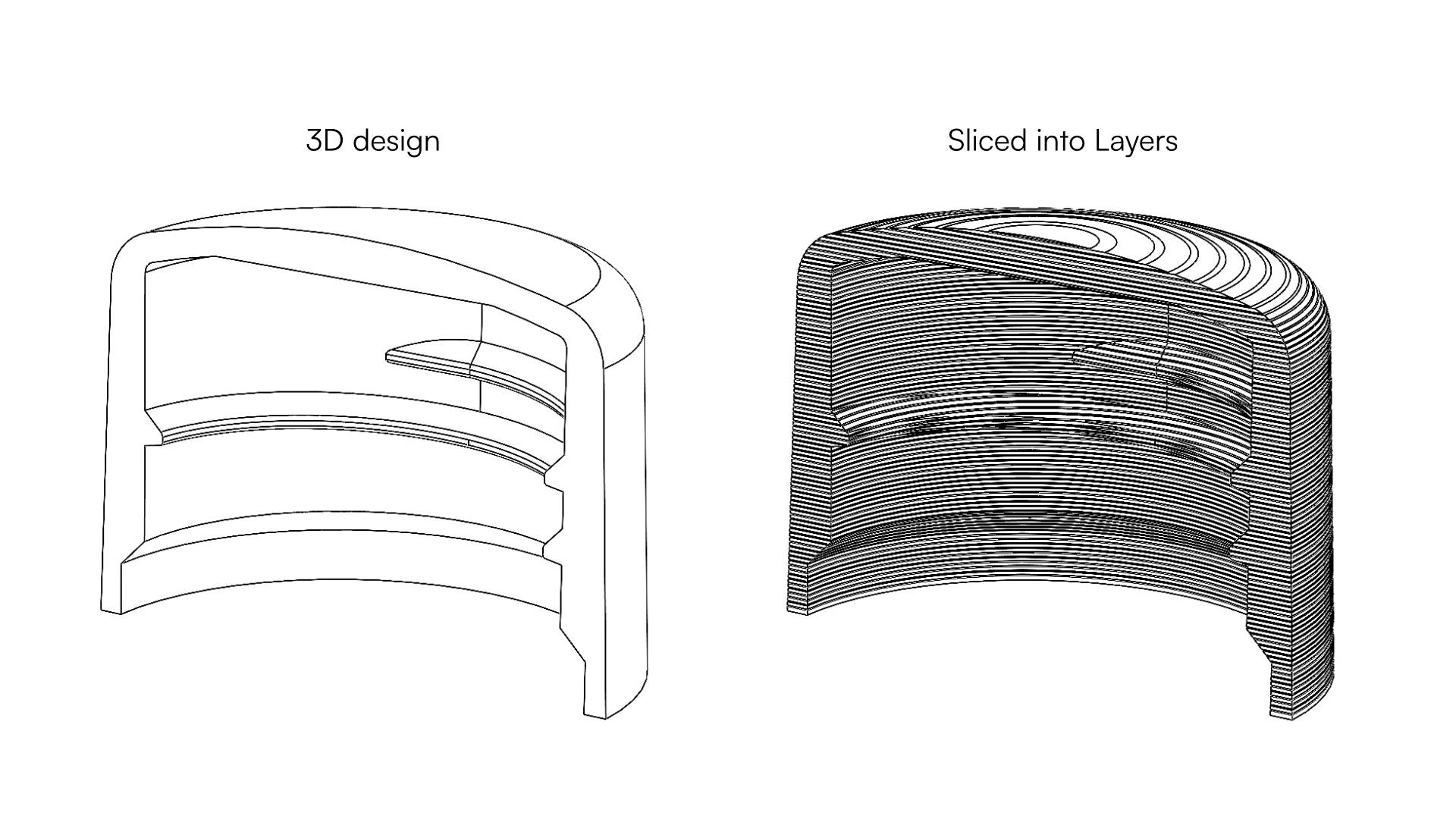
With resin 3D printing, the LCD Projector is responsible for curing the required area to make the final shape. The rest stays liquid. As the plate moves up, layer by layer the final 3D form takes shape.
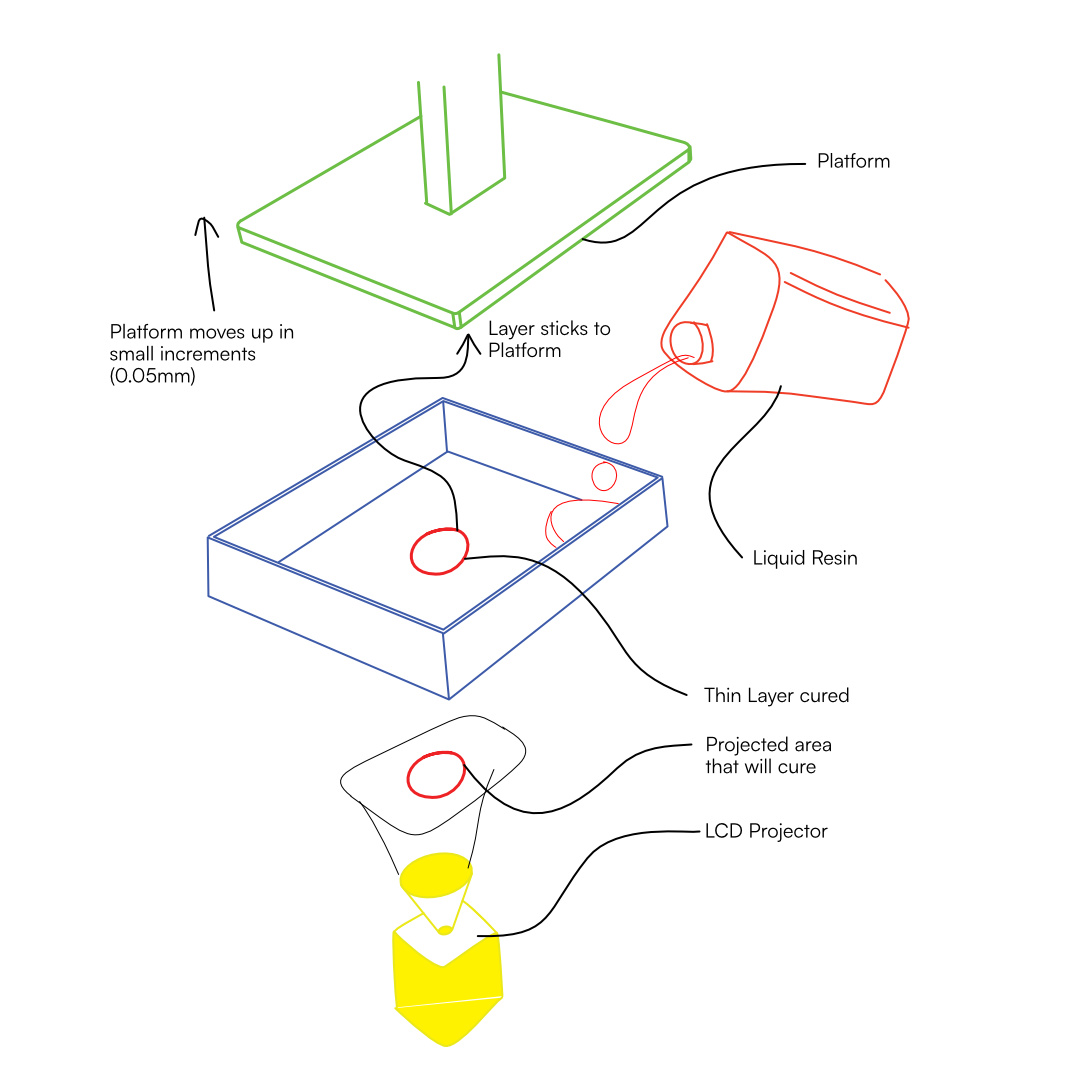
The plate moves up in tiny increments as the LCD projector cures the layers and you end up with the final part stuck to the bottom of the Platform.
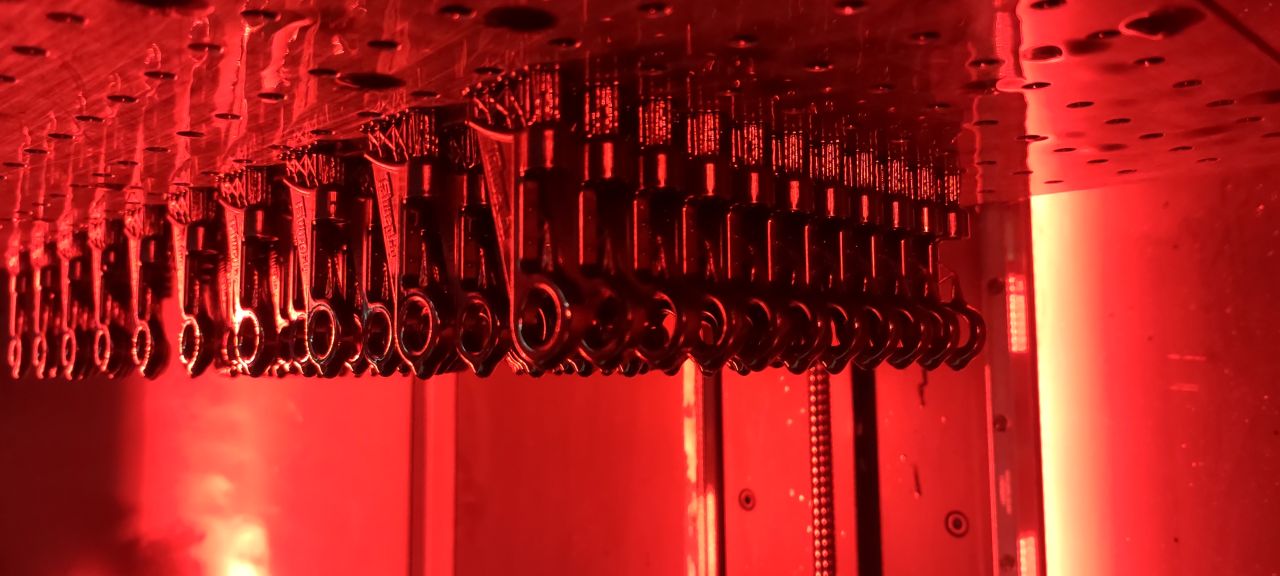
Robust parts for mass production
How strong are resin 3D prints?
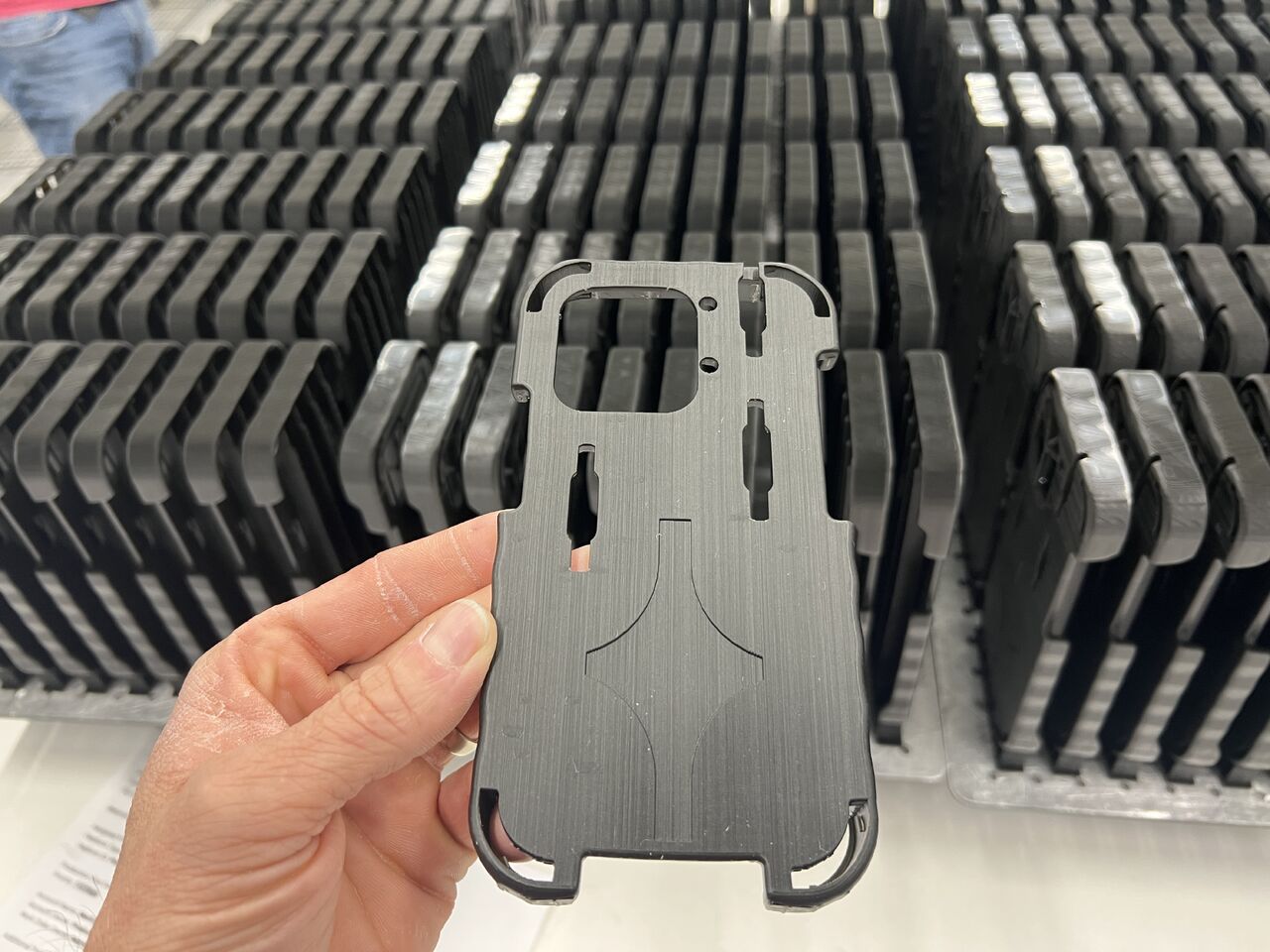
Historically, resin 3D printers have been unreliable for parts that need to be robust and functional. Resins that were producing functional parts were too expensive for mass production. These resins have been used by dentists for many years and we all know how 'cost-effective' dentists are ;)
Spencer has been working with leading resin manufacturers testing dozens of innovative materials. They have managed to curate robust, and cost effective resin formulas that he and his team at Merit3D use in the real world. Providing functional parts, just as an injection moulded product would.
Say no more to brittle resin prints.
The material science has caught up with the 3D printing technology and parts can now be robust and cost effective.
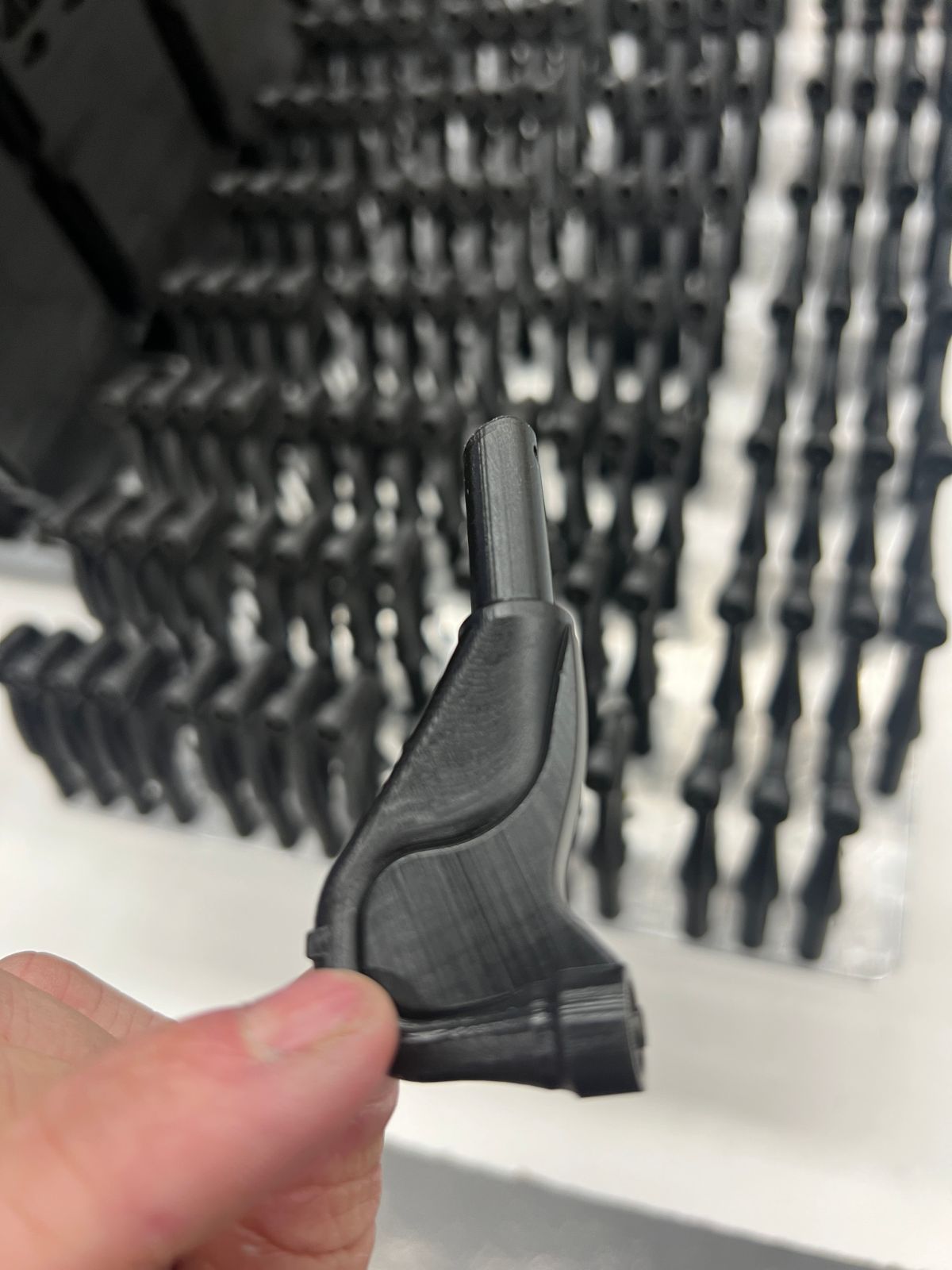
Surface finish of resin 3D prints
With plastic moulding, it's possible to achieve a perfect mirror surface finish, and detailed texture.
While 3D printing does not have the best reputation for surface finish.
Resin 3D printing is leading the surface finish charge.
3D printers create the part by curing layer after layer. These layers can be an eyesore. With resin printers achieving incredibly thin layers, these layers on the products are much less noticeable and Spencer's customers are not worried.
Can resin 3D printing achieve a mirror polished surface finish like injection moulding?
No. But it turns out. That's okay! Many products don't even need a mirror finish to function. The customers are not concerned.
So let’s talk a bit about Textures
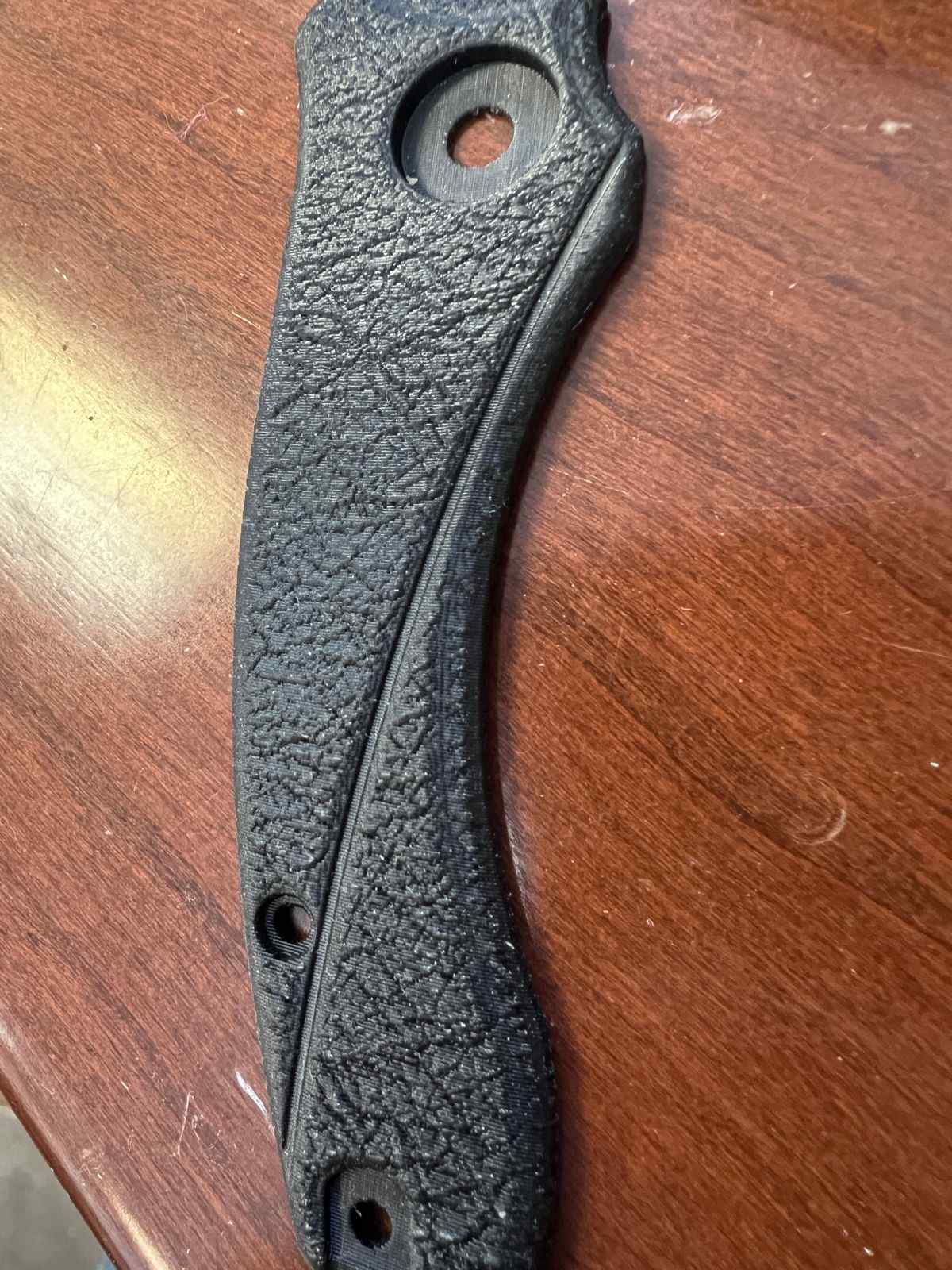
Many products come with different textures, and patterns. This helps us distinguish between parts and creates an interesting product aesthetic.
When using injection moulding. If you want a texture, you have to be extremely careful when deciding what and when to add it, because once you cut a texture or pattern into a mould, it’s very difficult to go back.
Textures and patterns are limitless with resin 3D printing.
In resin 3D printing. You can experiment with different textures and patterns without having to fork out any extra cash to pay for mould updates. You can even try a variety of textures and patterns at the same time. Giving you physical samples to help you decide
Have a look at some texture options on FAQ number 7: Merit3D
Surface and Textures
Options for available with resin 3D printing
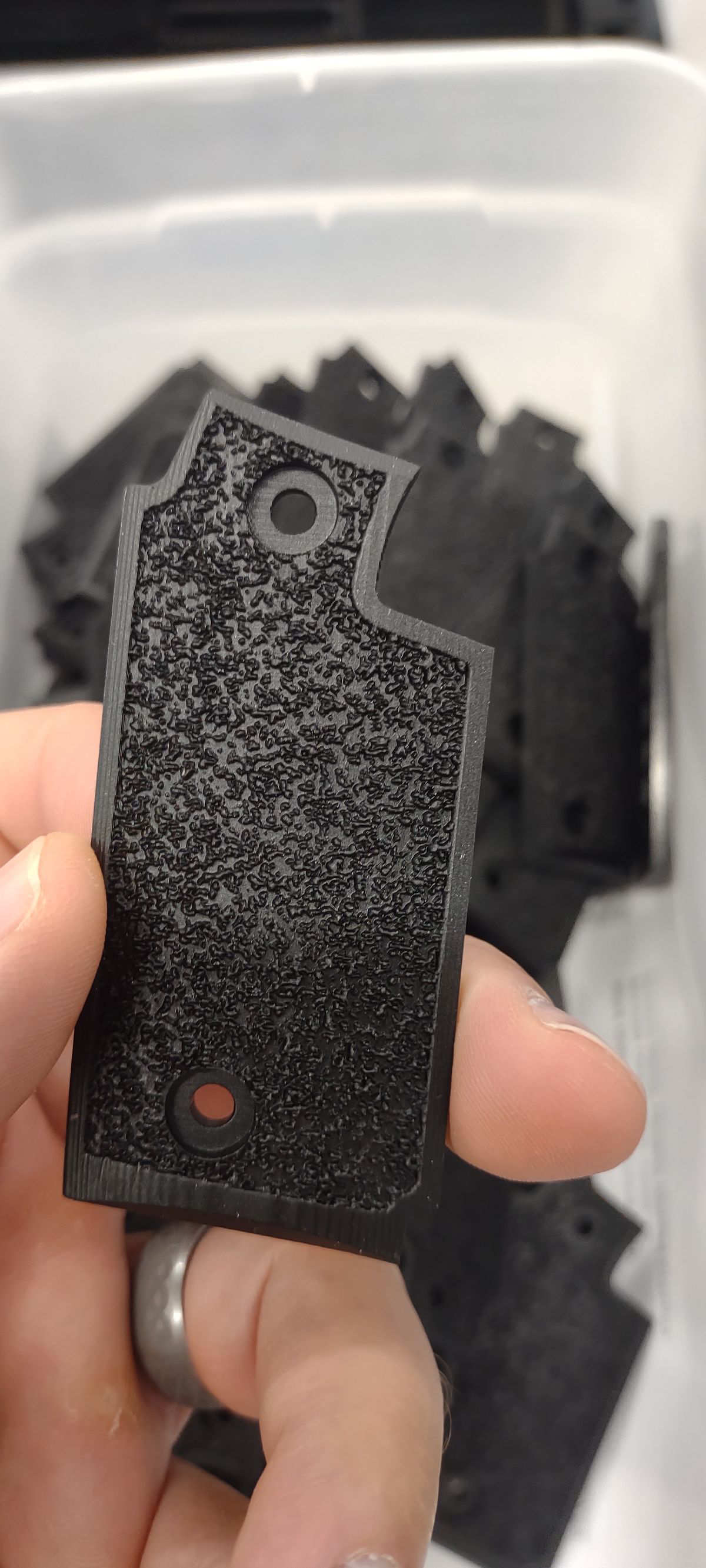
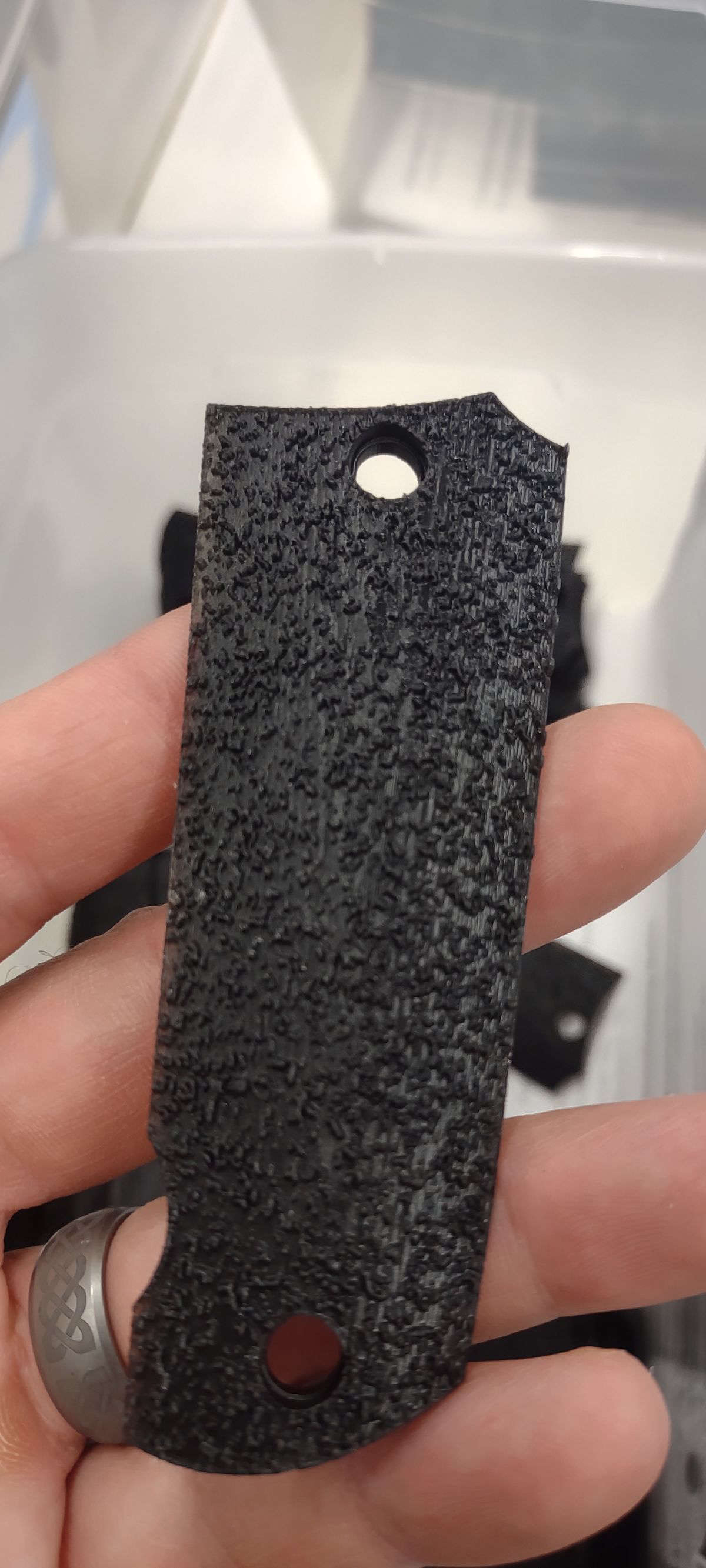
When to use Resin 3D printing for mass production
Injection moulding isn’t the answer to every product.
Resin 3D printing is not the answer to every part.
Where is the sweet spot?
Size:
The size of an apple or smaller seems to be the sweet spot.
Moving up to grapefruit size, still works, but less ideal.
Bigger than a grapefruit, things start getting challenging, but not impossible.
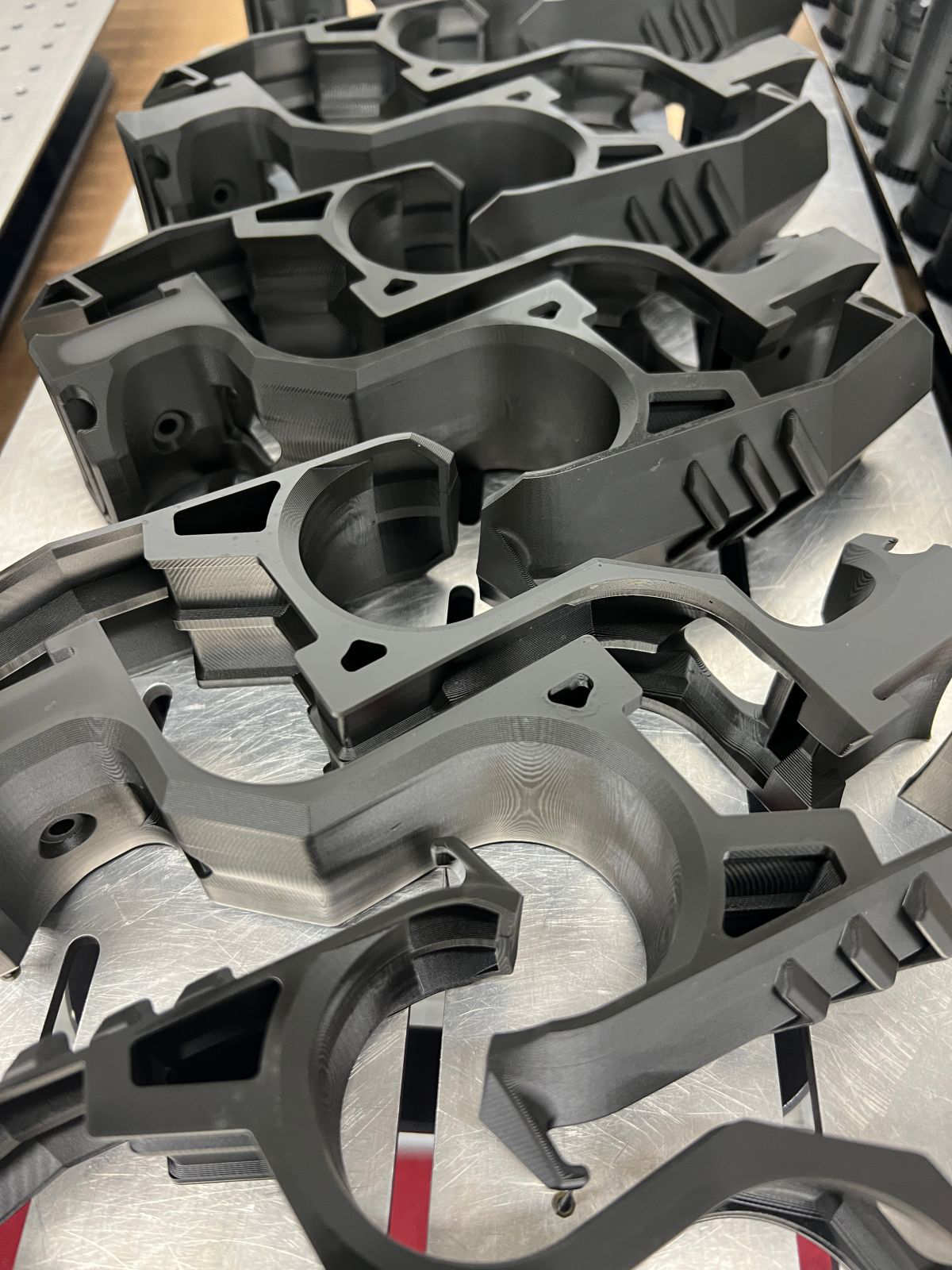
Functionality:
Where and how is your product going to be used?
If your product requires high impact and protects human lives (like a helmet). It might be worth waiting a few more years until the materials are proven.
Something like a door hinge, or helmet buckle where the product is mostly functional. Resin could be perfect.
Colour:
At the moment, colours are a limitation. If you need something in a specific colour resin might not be the best material.
"You can have any colour as long as it's black"
Explore the colours available before choosing resin 3D printing for production.
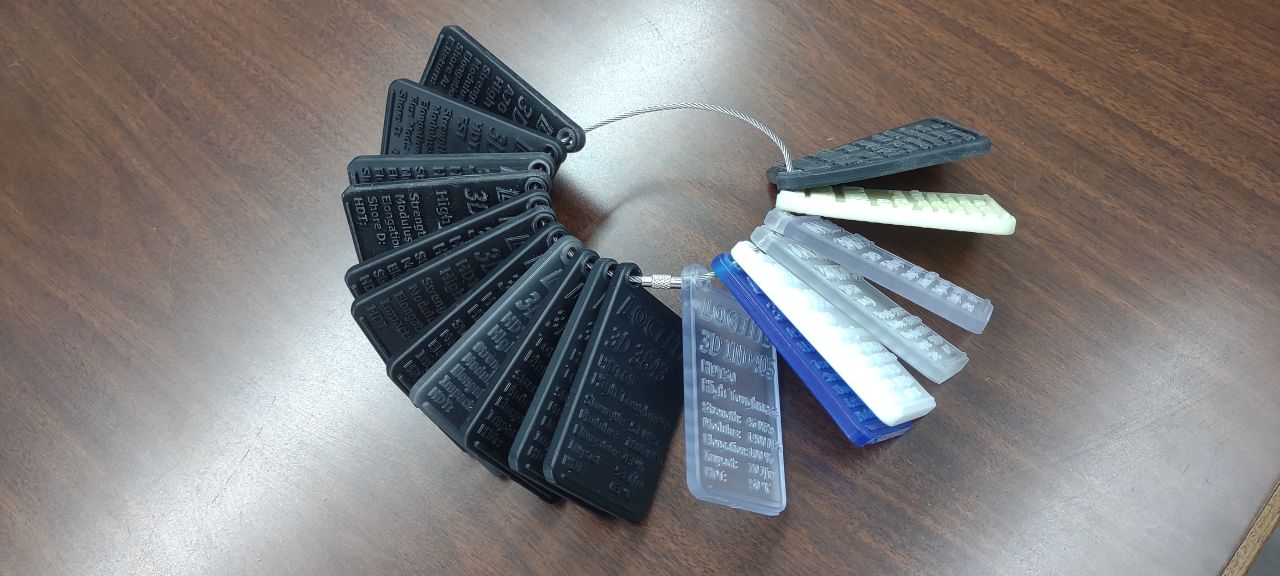
Quantity:
The smaller your part, the more can fit onto the 3D printing platform, the cheaper and more you can grow in an hour.
With parts the size of an apple or smaller, anything less than 150 000 units are showing to be economical.
Location.
Merit3D is based in Utah, USA. If you or your market are located in USA, great. Anything else. The shipping and duties need to be considered. Just like any other product when you are planning your production.
So, what is the perfect resin part?
- If you have a product that is mostly functional,
- aesthetics aren’t too much of a concern,
- size is smaller than an apple,
- you need between 10 000 to 100 000 parts,
- and you love black.
Resin 3D printing could be your perfect choice for your production!
Head to Merit3D to start the conversation. They are more than happy to assist.
Other Articles
More from the blog
Discover everything you need to know about taking your product to market.
Ready to turn your dream into reality?
Get customized product development assistance