In your design,
every part needs to be manufactured,
and assembled.
All these add up and cost money.
How do we save money and produce a cheaper product?
Lets explore:
- Reduce part cost?
- Are fasteners worth using?
- Why you should trust your manufacturer
- Should you add a bottle opener?
- When to design for manufacture?
- Why is Neo here?
Can you use one manufacture process to achieve multiple results?
Using one manufacture process for two product features.
One key area to save money is finding features and parts that can be grouped into one manufactured process.
This is easier said than done.
Find the features that are absolutely necessary for your product. Then look at what else that feature could do.
For example..
I’m building a product that needs shelves AND airflow. It can be expensive to cut holes for airflow. So how could I eliminate or reduce the amount of cutting we need to for airflow?
That question lead me to the shelve cutouts.
We have to cut a groove for the shelves so cut them a bit larger and use as air vents out the back of the unit.
Kill two birds with one larger cut:
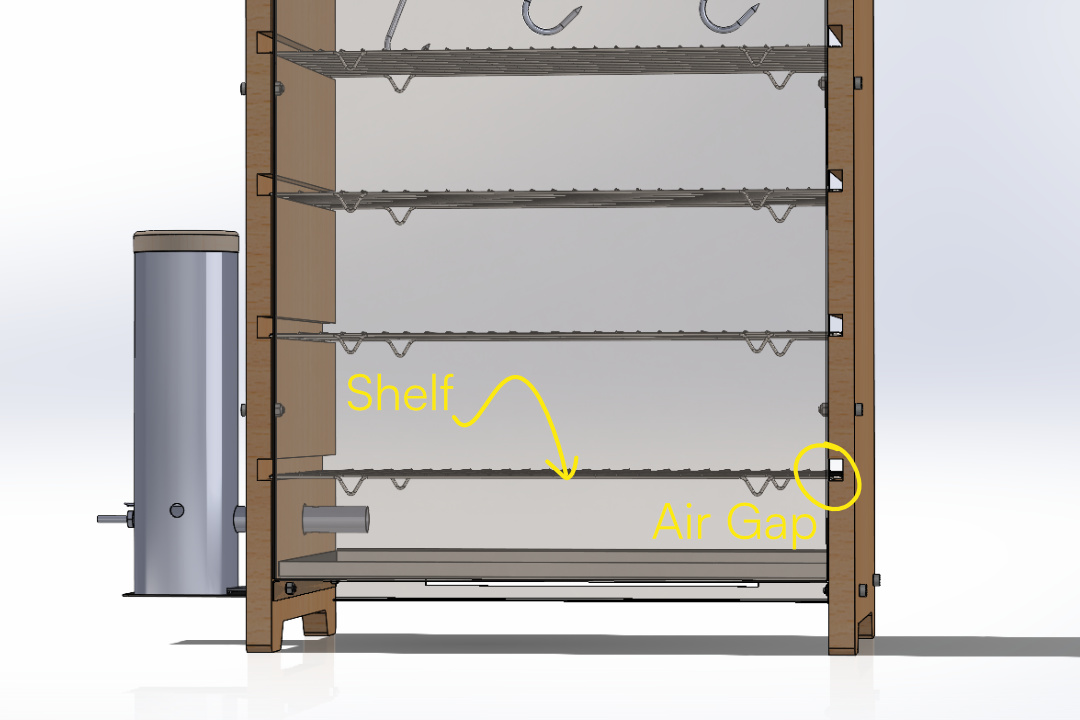
Can you eliminate parts and improve the design for assembly?
Remove the amount of fasteners in your design.
Its easy to use fasteners (nuts, bolts, screws, rivets, etc) for everything.
Fasteners are a simple solution. But they do add additional parts and processes.
When developing anything new. You control the design, giving you freedom to design your own features. Swap a fastener out for a ‘snap fit, or ‘press fit’ or ‘friction fit’ join.
Eliminating the cost of fasteners and saving money, by reducing assembly time.
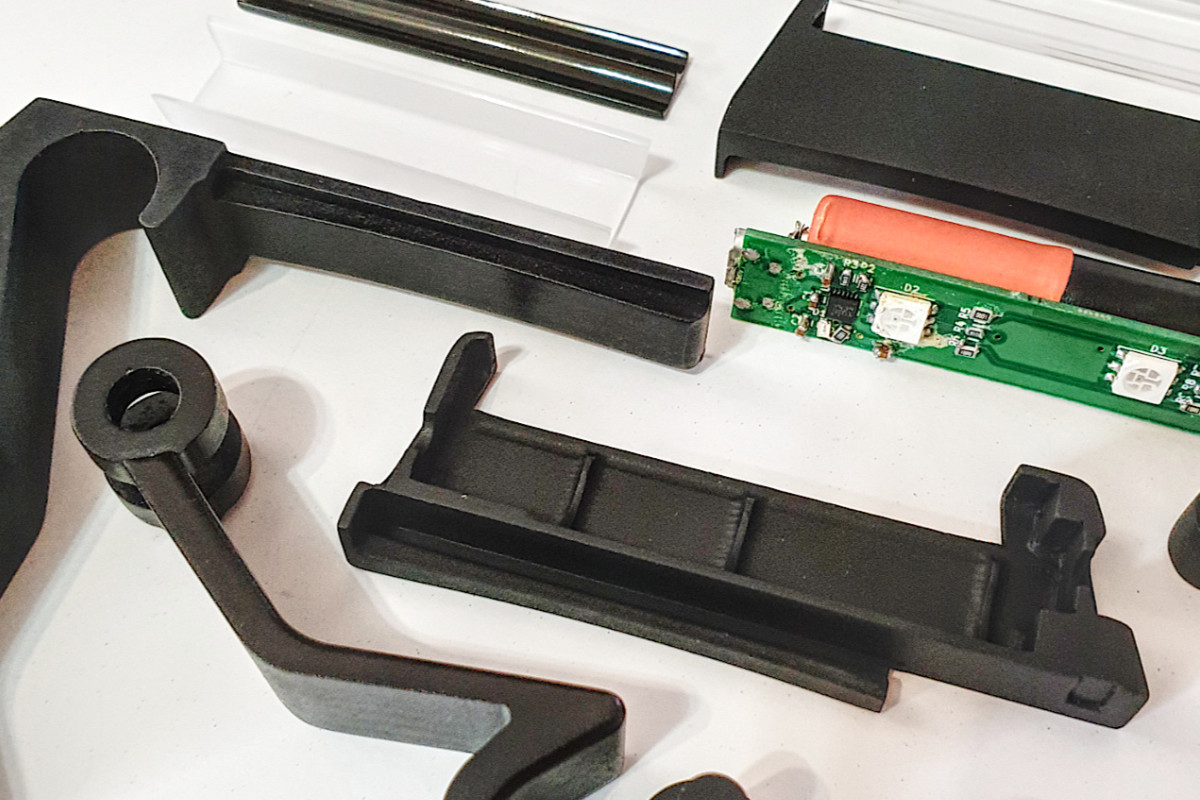
Merging plastic parts - When two become one (thanks Spice Girls)
When using plastic injection moulding as your manufacture process. You have freedom to design whatever you want.
You could merge two parts into one part. Reducing labour in assembly, number of parts and things that can go wrong.
The skills of the design and engineering team are critical when taking on these tasks.
It takes ‘out the box’ thinking and experience to turn two or more parts into one part that can still be moulded and perform multiple tasks.
I think DMC does that sort of fancy merging design!
Elimination of manufacture and production processes
If your product needs plastic moulding, sheet metal parts and custom fasteners. You have multiple processes within your production that need to come together.
Choose to manufacture more parts using the same process in one factory. You can negotiate a better deal and be more cost effective.
For example.
If you have 5 parts that are manufactured out of sheet metal and 2 parts that need to be injection moulded.
If you can eliminate the 2 parts that need to be injection moulded and make them from sheet metal.
It could simplify production, potentially reducing cost and mistakes.
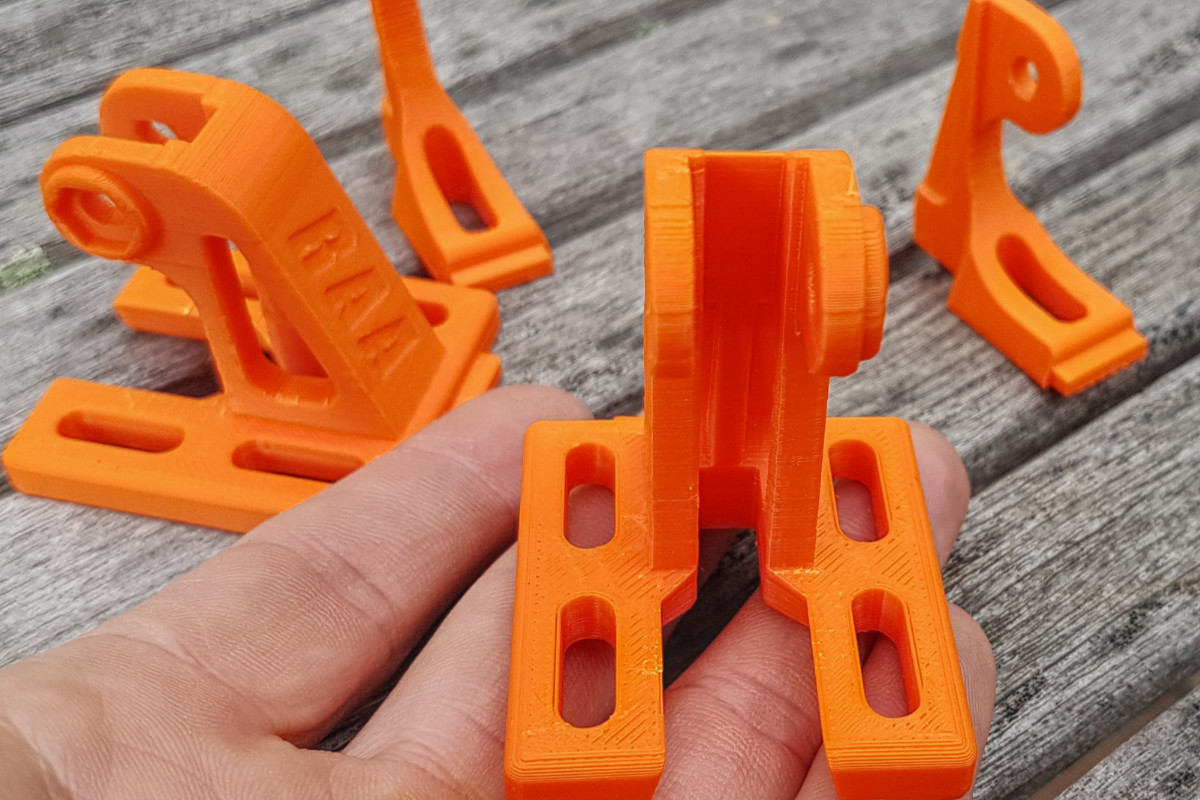
Lean on your manufacturer's experience
Over my last 200 products.
There has been a trend with successfully manufactured products.
The balance between the production factories design involvement,
and the design’s team design for manufacture abilities,
help create a successfully manufacturable product.
Designing for your manufacturer
Hiring experts and letting them get on with what they are good at is how we build amazing products and businesses.
It’s critical the design team can design for manufacture. Which many can do.
However, that last 5% of the detailed design becomes unproductive if the design team creates the perfect part for manufacture.
This is where the expert engineers from the factories know their stuff and should be actively involved in the project.
We’ve had incredible design suggestions from factories that help build a engineering master piece for production.
We end up saving time by letting the experts do what they do best.
Designing for manufacture review with the factory
Each part receives feedback and suggestions on how we can improve the manufactureability.
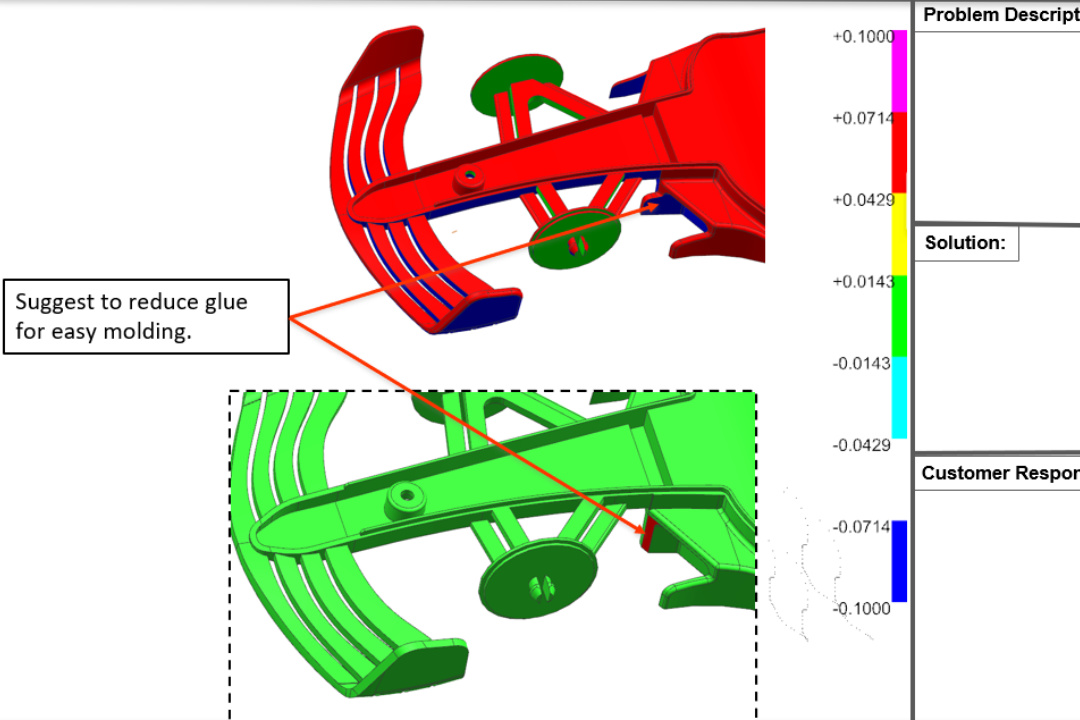
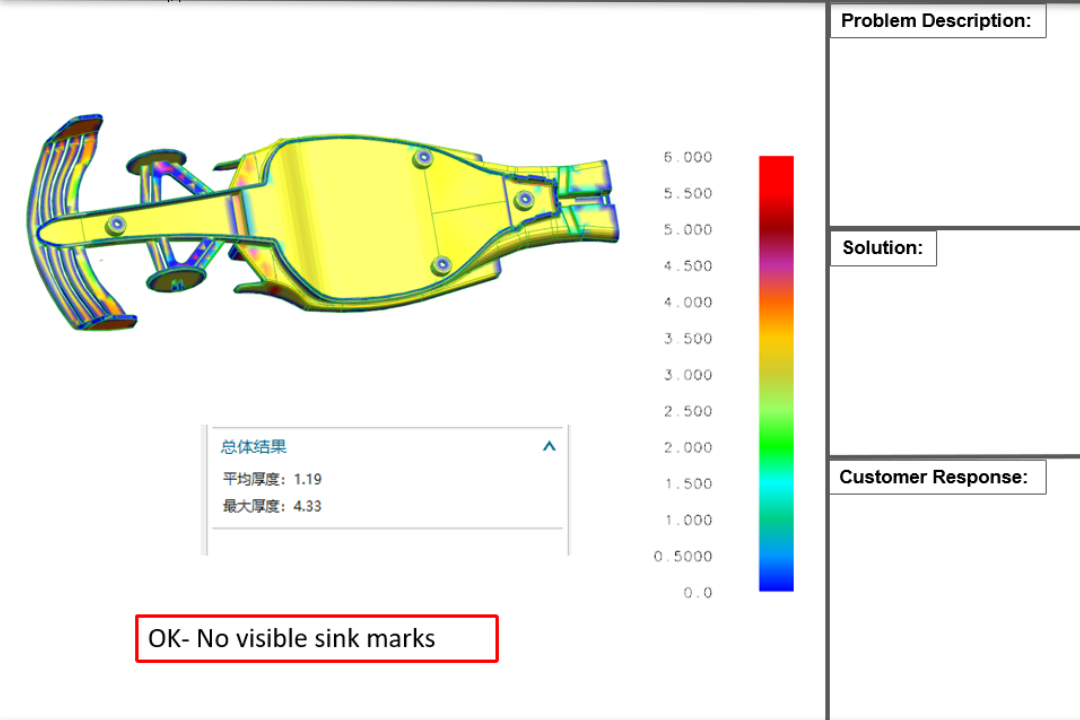
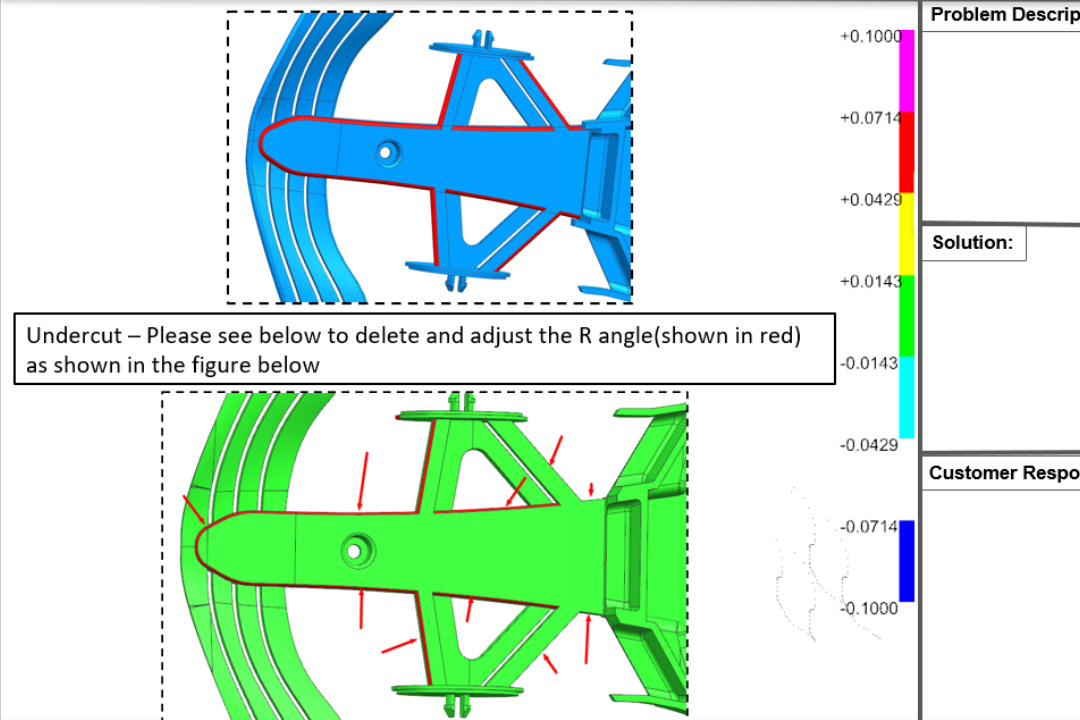
Finding the right manufacturer
In addition to the previous point.
If you rely on your manufacturer to help with the final design for manufacture.
You rely on their expertise.
And my goodness.
You better hope that they know their stuff!
This is where the Greats are separated from the Goods.
Expert manufacturers can make or break your product by helping you optimise for production in ways you didn’t even know were possible!
Find the right partner, treat them like a partner and reap the rewards.
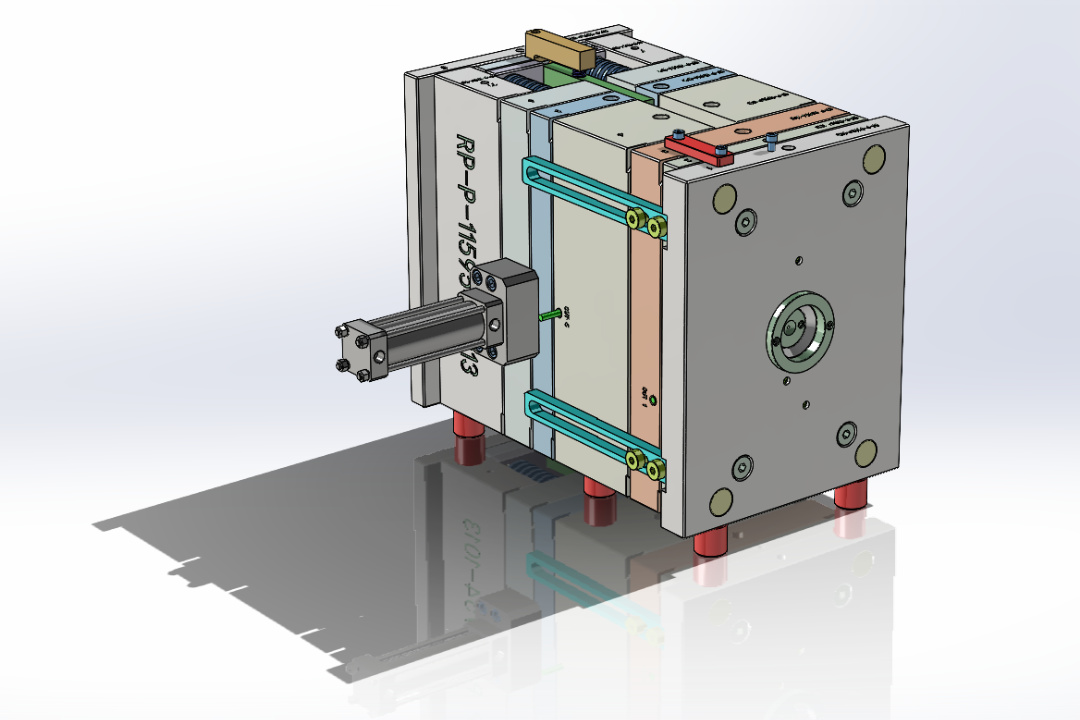
Focus on product features that matter!
Before you set off on this mission of building a physical product,
you had a dream,
a vision,
and a goal .
it’s tempting to add more and more and more and more (see what I did there, it's irritating).
Because you want your customer to feel like they are getting more and more value from your product.
Over deliver!
But more can hurt you and your bottom line…
It’s like putting a bottle opener on almost everything.
Is it needed?
No it’s not.
Stop it.
Okay, maybe just one. Kidding! No.
Choose the features that make the most sense for your product.
Focusing on what really matters to your customer, you spend more time, energy and cash on the things that matter. This not only helps save time and money, you end up improving the design further because that is what you’re focused on.
You end up with a better, cost effective solution that your customer loves.
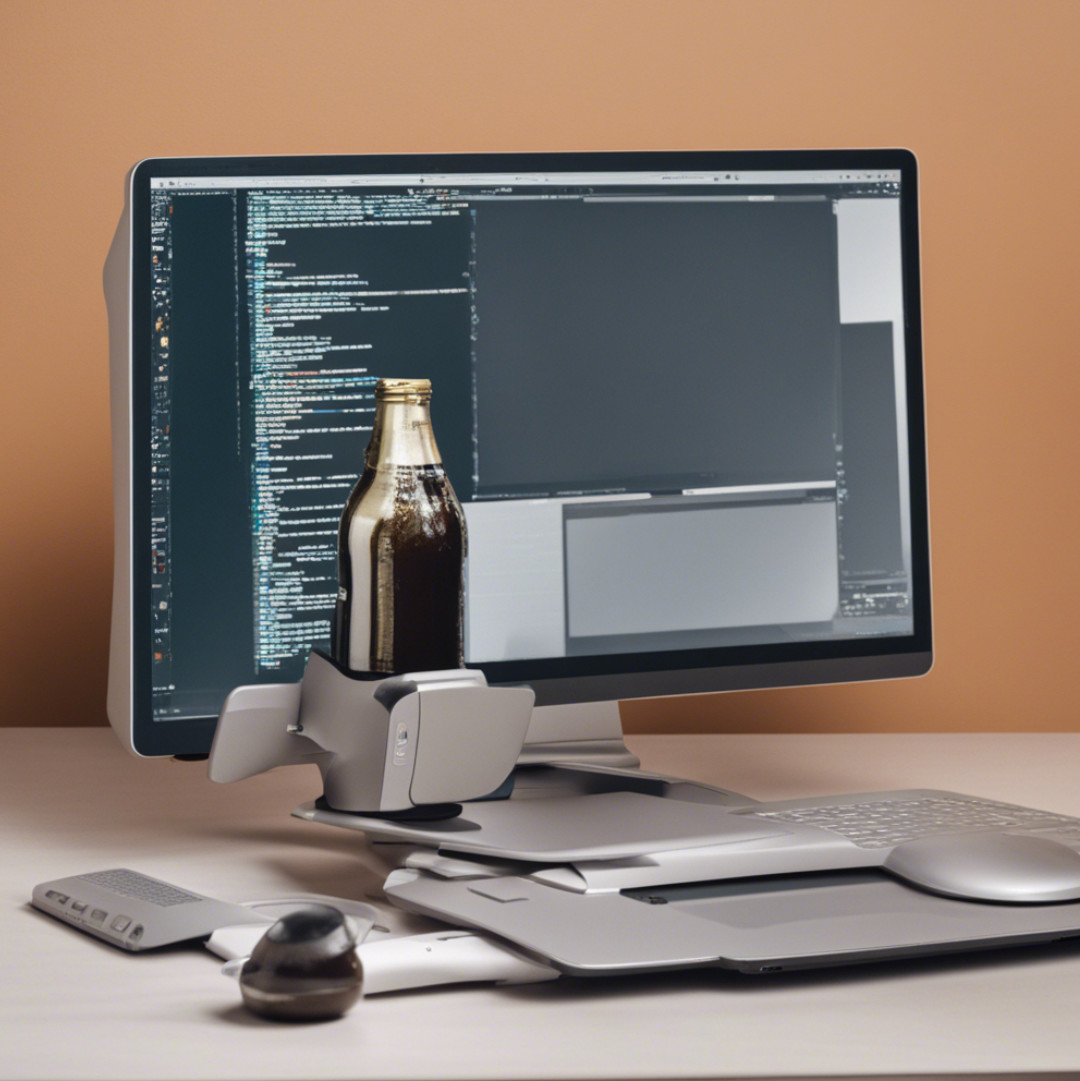
Use the right material and process for your product
Is your designer biased towards a manufacture technique?
I am an advocate for simplifying your production and number of processes.
But simplify too much and you can end up with a parts that are not optimised for production.
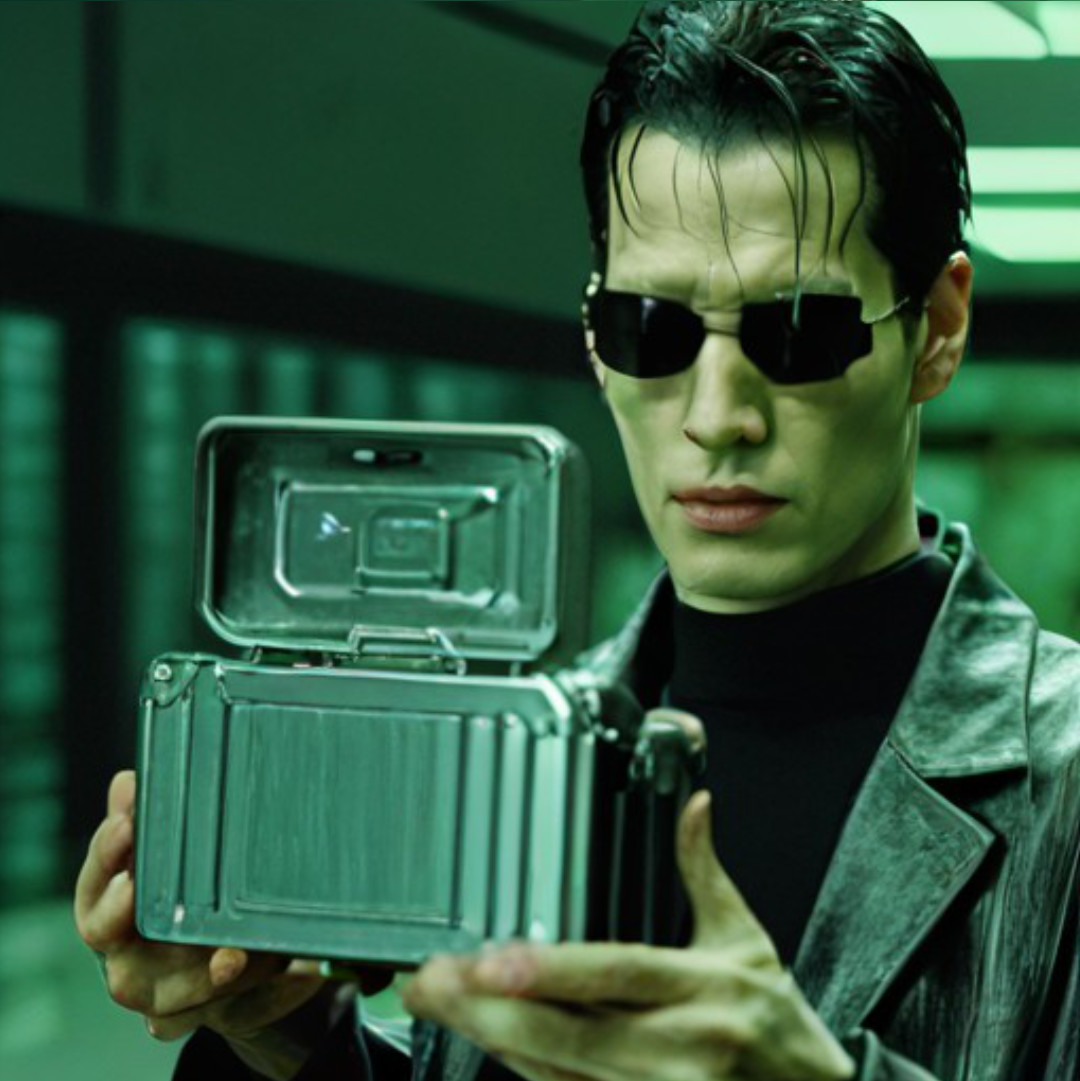
Here’s a story:
When I starting out my product design career. I spent many years working in sheet metal. It gave me this superpower of breaking down even the most complex shapes into sheet metal parts.
I thought this was brilliant, it felt like I was Neo. But it was actually a curse. And like Neo, I had to learn to control my sheet metal powers and learn other techniques.
Since then.. Myself and the DMC team spend many hours each month keeping up with new techniques.
Always searching for the right manufacture technique for the part, product and client.
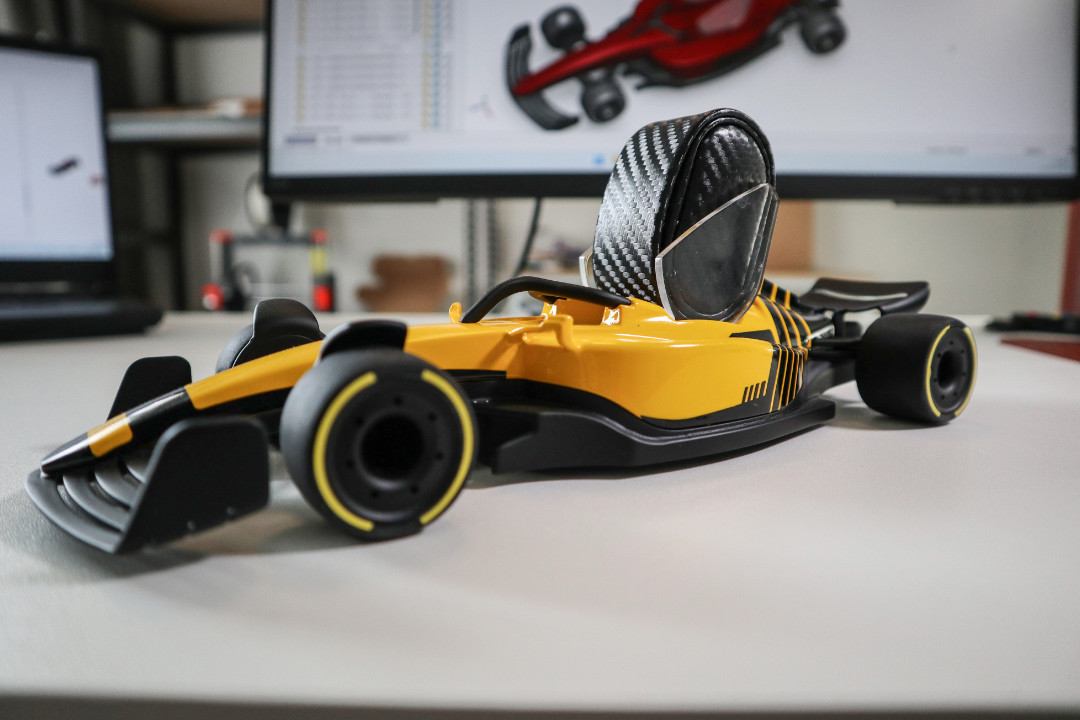
What you can spend designing and manufacturing your product
Sometimes it’s not the part that dictates the material and manufacturing.
Sometimes it’s your budget.
If you have limited resources, you might not be able to use injection moulding straight away…
If you have a set amount of money, or a time constraint. The design needs to adapt and work within those constraints.
Understanding what you want to spend is key to actually finishing the design of your product and getting it to your customer.
What’s better?
An amazingly well-designed product, but no money to make the moulds?
Or an average looking designed product, does the job and you can make 100 units to test with your customers in 2 months?
The answer is….
it depends on you and your business and goals.
Design for manufacture from the beginning
I’ve found two key stages in designing a product.
The first is when you learn, build and prove the design enough before you spend all your money.
The second is when you feel confident in your design and now refine the idea into a working prototype.
In both these stages it’s important to think about design for manufacture.
Design for manufacture can mean different things.
Yes, in stage 1, let’s not care about how the plastic parts will be moulded, or what draft angles we’ll use, or what metal thickness we need.
But. Thinking about how the product is manufactured is as much part of the success, as the idea itself.
It’s how to design a product that makes a profit or makes a killing.
If you integrate the manufacture plan from the start, you craft a solution that takes your goals into consideration.
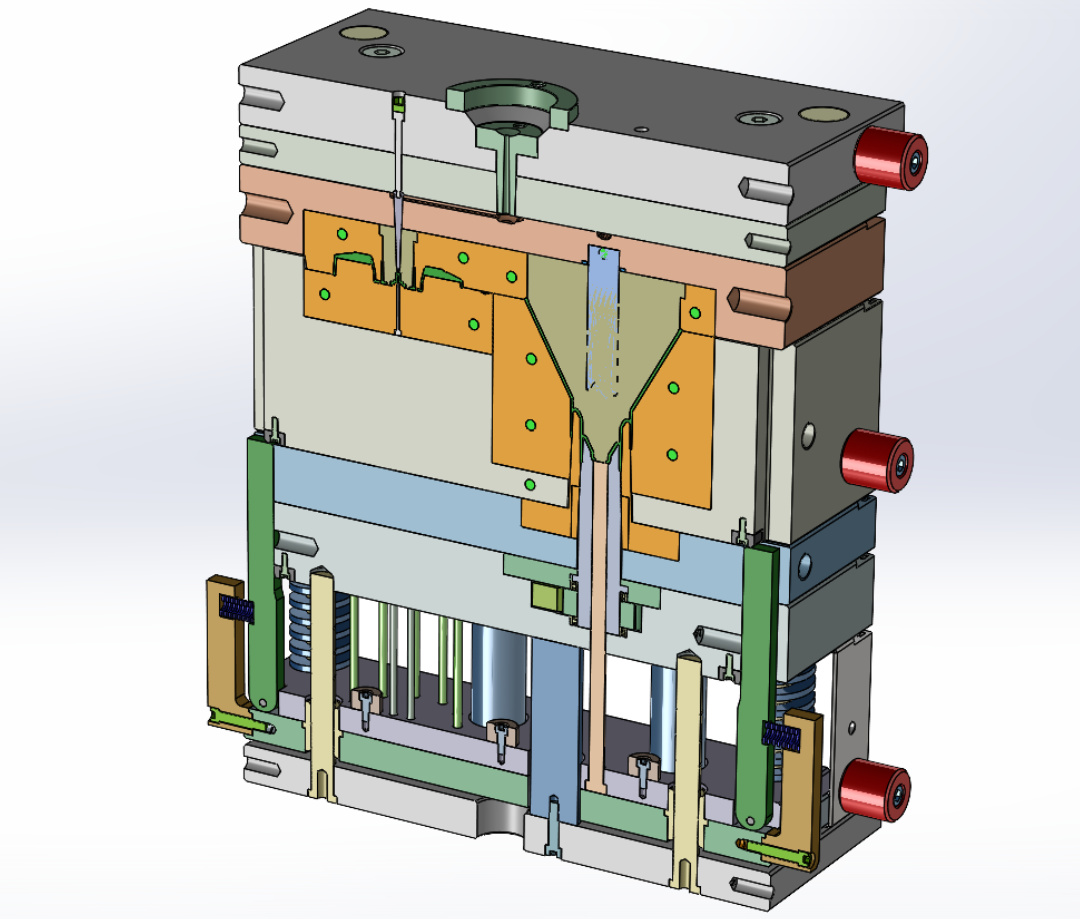
For example: We designed a coffee brewer. And from the start of the project. We knew one of the selling points would be the price. So we made sure that the material and manufacture techniques were designed for mass scale. Yes we had to let the manufacturing method decide a little on how it looks. But to make the product work in the business, we had to prioritise function and manufacture, and not as much aesthetics.
Cash, Launch, Quantity, R&D, Budget, Skills - all count towards the initial idea and these should all be part of your ideation.
Designing for manufacture is not just draft angles, material choice and what technique to use.
Its about every decision, from the beginning.
That's how you deliver a product that supersedes your cost target!
Other Articles
More from the blog
Discover everything you need to know about taking your product to market.
Ready to turn your dream into reality?
Get customized product development assistance